Hydration is the inevitable choice for the technical development of automobile coating industry!
In recent years, the automotive industry has experienced earth shaking changes. The popularity of SUVs, the advent of the era of new energy vehicles and the trend of lightweight... In fact, many enterprises still have a long way to go in their investment in new energy vehicles and lightweight, involving many issues such as material selection, production efficiency and price. However, there have been significant changes in automotive coatings.
From the feedback from the market, consumers have strict requirements for environmental protection when purchasing coating products. They will not only understand the content of harmful substances in the products in detail, but also give priority to products with various environmental protection certification. Automotive coatings are developing towards environmental protection and improving the appearance decoration effect of the whole vehicle. The coating process tends to multi-layer composite coating. There are many kinds and a wide range of coatings used in the automotive industry, including automotive body coatings, container coatings, frame and other component coatings and special coatings. In particular, the coatings applied to the body coating of passenger cars represent the highest level of the coating industry due to their high performance requirements.
Now, domestic automotive coatings are mainly solvent system, and the restriction on VOC has become an important index of automotive coatings. The VOC emission of traditional solvent based coatings is about 125g / ㎡, and that of water-based coatings is about 27g / ㎡. Taking the current popular flash coating as an example, its VOC emission accounts for 66% of the total. If water-based coatings are used, the VOC emission of the whole vehicle can be reduced by more than half. We hope to present the changes taking place in the automotive coating industry from the perspectives of cost, process and environmental protection.
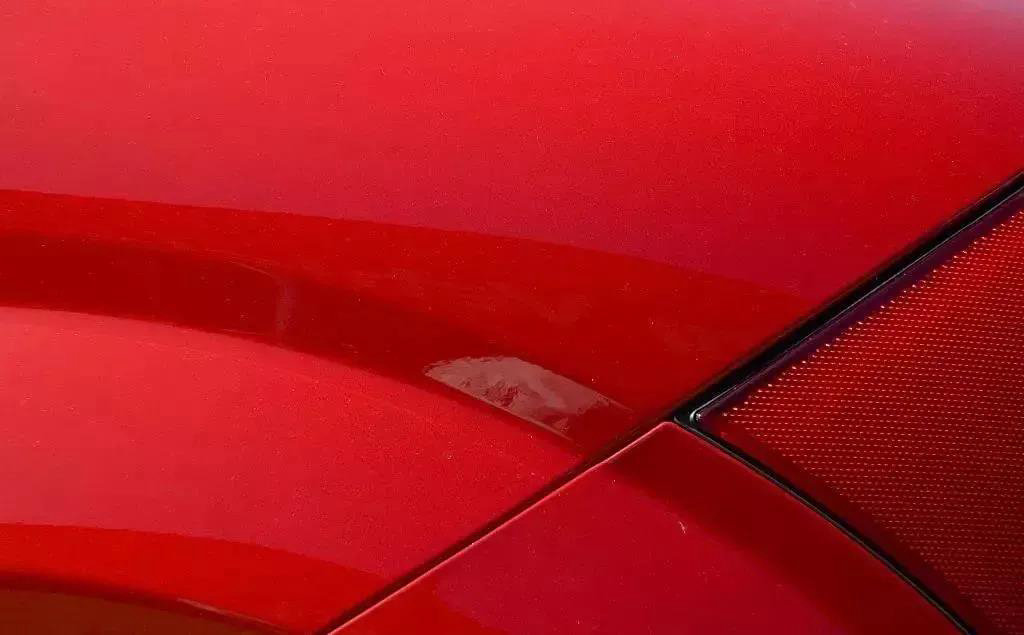
Classification of body coatings
Primer
Automotive primer is the first coating directly applied to the surface treated body surface.
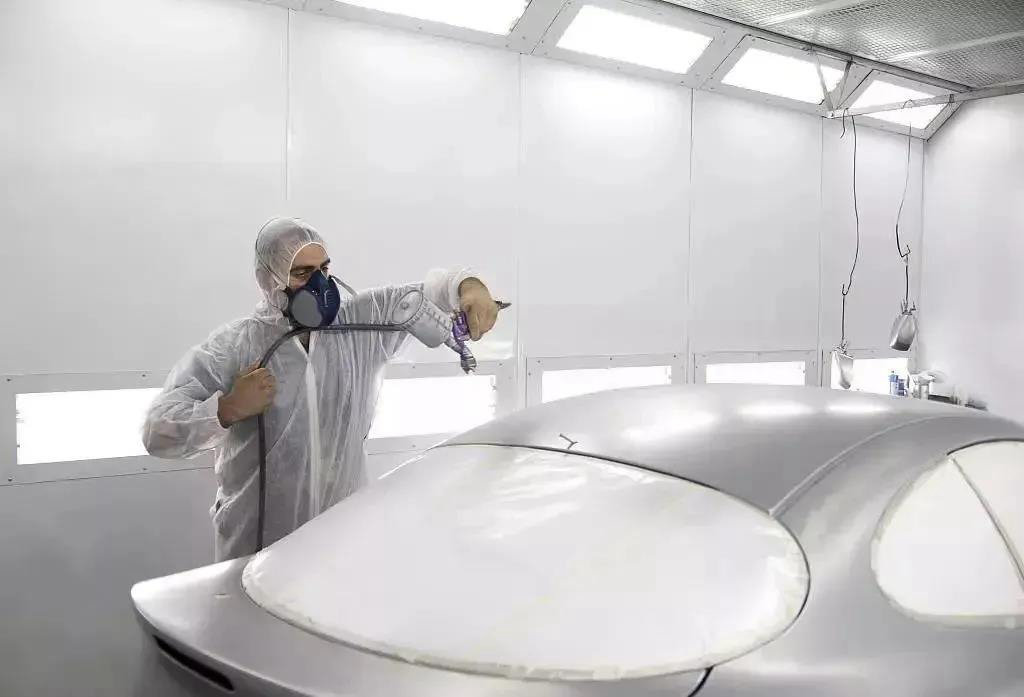
present situation
According to the application position of the primer on the vehicle, the primer is required to have good adhesion with the substrate and good compatibility with the upper intermediate paint or finish paint. In addition, it must have good corrosion resistance, rust resistance, oil resistance, chemical resistance and water resistance.
At present, cathodic electrophoretic primers are used in almost all passenger cars in China, and traditional alkyd, phenolic or epoxy primers are also used only on some passenger cars and trucks. Electrophoretic paint is developed on the basis of water-based dip coating primer. Commonly used include epoxy resin paint, alkyd resin paint, amino resin paint, phenolic resin paint, etc; Pigments generally use iron oxide red, titanium white, carbon black or other pigment fillers. The film thickness is generally 20 ~ 35 microns. Generally, the painted area of cathodic electrophoretic paint for passenger cars can reach about 120 square meters.
Development trend
In the future, the development trend of primer can be summarized into three directions: low VOC, no intermediate coating and low film thickness. Although electrophoretic coatings are waterborne coatings, they still contain a certain amount of organic solvents. At present, the solvent content of the latest cathodic electrophoretic coatings has been reduced from 2% ~ 3% to 0.4% ~ 1.8%, greatly reducing VOC emission. In order to reduce the coating cost and simplify the coating process, some automobile manufacturers have adopted the coating process without intermediate coating, but the cancellation of intermediate coating puts forward higher requirements for the flatness of electrophoretic primer and the thickness of finish coat has also increased. The reduction of film thickness is mainly realized by cathodic electrophoretic paint with high permeability and high corrosion resistance. Generally speaking, this method can reduce the amount of paint by more than 13%. At the same time, the corrosion resistance of the paint film shall not be reduced. For example, the thickness of the primer paint film can be reduced to 15 microns on the outer surface and 9 microns in the inner cavity. The corrosion resistance and flatness of the paint film are equivalent to that of 22 microns on the outer surface and 12 microns in the inner cavity. In addition, the development trend of primer also includes the application of lead-free Wuxi coating, low-temperature baking coating, weather resistant coating, etc.
Middle coating
Intermediate coating is also called secondary slurry, including putty, secondary primer and sealing paint.
present situation
At present, putty is no longer used in new car production, but only for car repair. In China, commercial vehicles such as trucks and mini vehicles generally do not need intermediate coating, but directly apply overlay paint on the primer. Plastic parts and parts do not need intermediate coating, such as bumper or vehicle chassis. However, intermediate coating is required for the outer body of both passenger vehicles and commercial vehicles and their later repair. Intermediate paint is used for the coating between automobile primer and topcoat or primer. It plays the role of connecting primer and topcoat, can provide protection suitable for topcoat, and has leveling property to improve the fullness of the whole paint film. Common intermediate paints include polyester resin paint, amino resin paint, epoxy resin paint, polyurethane resin paint, etc; The pigments and fillers are titanium white, carbon black, barium sulfate, talc powder, silica, etc. The thickness of intermediate coating is generally 20 ~ 30 microns. At present, many intermediate coatings are still solvent type.
Development trend
In the future, automotive intermediate paint will mainly develop in the direction of high solid differentiation, hydration and powder. At present, the main development direction of automotive coatings in the United States is high solid differentiation. High solid mid coat is prepared by high solid polyester, polyurethane, amino and other resins. Its construction solid content can be higher than 60%, or even 70%, which is 10% ~ 20% higher than that of traditional mid coat, and VOC emission can be reduced by 20% ~ 30%. In order to meet the requirements of low VOC emission, the newly-built automobile coating line in China generally adopts water-based intermediate paint, such as water-based polyester amino paint and water-based polyurethane paint, and its construction solid content generally reaches 50% ~ 60%. Although powder coating is one of the coatings with the lowest VOC emission, it has not been used due to difficult color change and other reasons. At present, except for individual vehicle parts production lines, there is no precedent for the use of the whole vehicle in China. However, with the improvement of spraying equipment and the maturity of powder slurry technology, this coating technology will become one of the choices of automobile manufacturers in the future.
Topcoat
Automotive finish mainly plays a decorative and protective role in the whole automotive coating, generally including finish paint and color paint.
present situation
Automotive finish paint shall generally have bright colors, good mechanical properties and excellent weather resistance. Generally speaking, both passenger cars and commercial vehicles, whether parts, plastic parts or later maintenance, need topcoat coating, but commercial vehicles generally only spray bottom color paint, which is no longer covered with finish paint, while parts generally do not spray bottom color paint, but only finish paint, and this finish paint is sometimes replaced by other anti-corrosion paint.
At present, amino resin, alkyd resin, acrylic resin and polyurethane resin are mainly used as base materials for high-grade automobile finish. Organic and inorganic pigments with bright color and good weather resistance are selected, and some additives such as UV absorber, leveling agent, anti shrinkage agent and resistance regulator are added to achieve satisfactory appearance and performance.
Development trend
In the future, the development direction of topcoat is hydration, powdering and high solid content. The supporting process of "primer + varnish" is usually adopted for water-based finish paint. Since solvent based primer is the largest source of VOC emission, accounting for about 50% of the total emission of each process of automobile body coating, if the primer is changed to water-based paint, VOC emission can be greatly reduced. However, the water-based topcoat has not been widely used until now, mainly due to the high weather resistance and decoration of the water-based topcoat and the poor solid sub topcoat. At the same time, because it still contains 2% ~ 15% organic solvent, it has high requirements for construction environment and drying conditions and high comprehensive cost. However, from the perspective of development trend, solvent-free waterborne coatings will still become the main development direction in the future. At present, acrylic resin powder coating is mainly used for powder finishing paint. Although its cost is significantly higher than that of two-component polyurethane varnish, it saves the operation cost of waste residue treatment and VOC treatment. With the expansion of production scale, the cost of raw materials is further reduced, and its direct cost will be further close to that of two-component polyurethane varnish.
Consumption trend of domestic automotive coatings
Passenger car coating
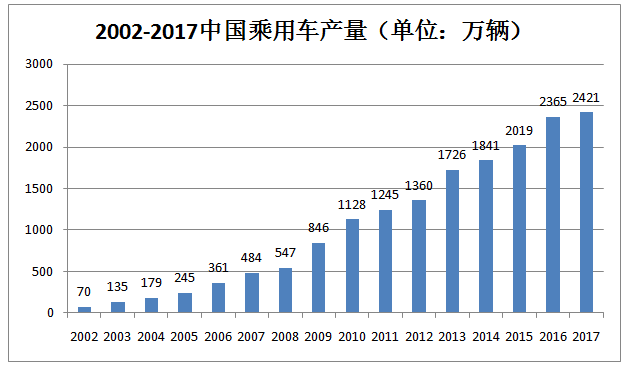
The growth of domestic passenger car coating consumption is mainly driven by the growth of automobile sales, while the consumption of single car coating is gradually declining due to the application of new coating processes and materials. Among them, the fastest decline is German passenger cars, followed by American cars. Japanese, Korean and domestic independent brands decreased less due to the low base number of single vehicle paint.
The passenger car coating with the fastest growth in consumption in the future is the top coat, which is mainly due to the promotion of the middle coat free process in recent years, which requires the top coat to have the properties of both the middle coat and the top coat. In addition, the popularity of various metallic paints and pearlescent paints that need to be sprayed with multiple times of base coat, the film thickness of the top coat has a growing trend. The intermediate coating is affected by the non intermediate coating process, and the consumption of single vehicle decreases.
Coatings for passenger cars
As the domestic bus production begins to decline, the consumption growth of bus coating will slow down. From the perspective of single vehicle coating consumption, different from passenger cars, it is still improving steadily, especially the rapid growth of medium paint. This is mainly related to the increase of the proportion of large buses.
Domestic automotive original coating is a relatively closed market. The original coating is generally sold from automotive coating manufacturing enterprises to vehicle enterprises through direct sales, which leads to different prices for each coating of each automotive coating enterprise to different vehicle enterprises. The price of the same brand and specification of automotive paint sold to domestic cars and imported cars may differ by 50%. In recent years, there has been vicious price competition in the domestic automotive original paint market. Even foreign brands have to make substantial concessions in order to compete for market share.
Market demand of polyurethane coatings for vehicles
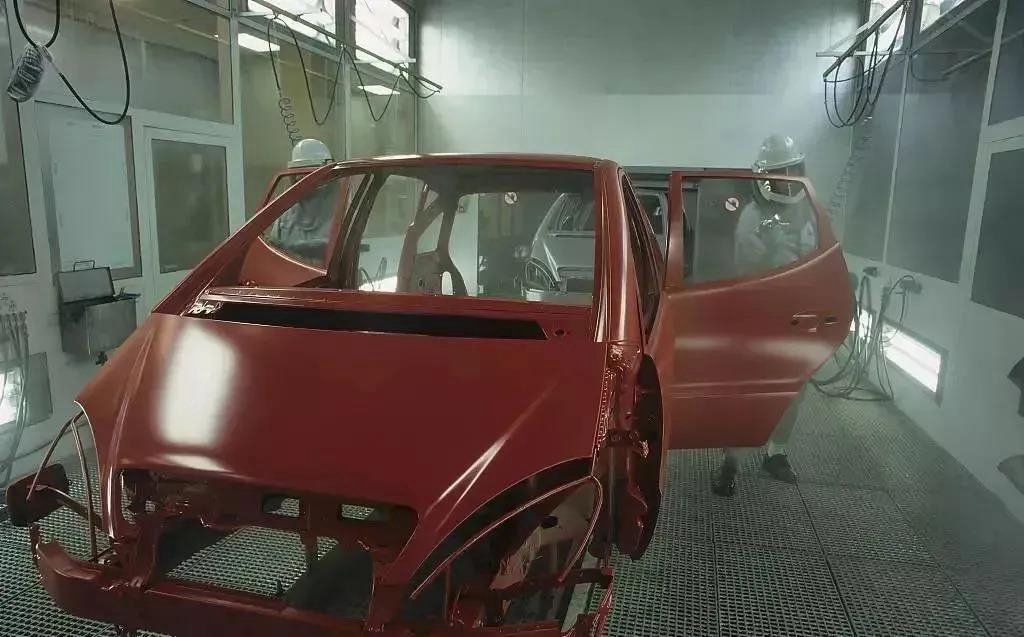
Consumption forecast
Polyurethane coating has the advantages of good wear resistance, corrosion resistance, chemical resistance, high hardness and high elasticity. It has a wide application and good development prospect in the field of automotive coatings. According to the latest research report released by market research future, the global polyurethane coating market consumption is expected to reach 3.7812 million tons by 2023, with an average annual compound growth rate of 7.3% from 2016 to 2023. At the same time, it will also increase significantly according to the market value. Polyurethane coatings can be divided into two-component polyurethane coatings, one-component waterborne polyurethane coatings, light curing waterborne polyurethane coatings, room temperature curing waterborne polyurethane coatings, the third generation waterborne polyurethane coatings (PUA), environmental friendly low aromatic polyurethane coatings, etc.
Development trend
In the future, the development direction of waterborne polyurethane technology in China will focus on the following aspects: strive to improve the mechanical properties, solid content and bonding strength of waterborne polyurethane materials, especially the initial bonding strength; On the basis of further reducing v0c, the crosslinking mechanism of waterborne polyurethane and the development of new crosslinking agents are carried out to improve the room temperature curing performance of waterborne polyurethane; Minimize the amount of organic solvent and finally achieve solvent-free; Solve the problems of poor fullness and low gloss of waterborne polyurethane coatings, develop high-performance coatings and actively explore new application fields; By further reducing the cost of waterborne polyurethane, the application problem of waterborne polyurethane technology is solved; Strengthening the basic theoretical research related to waterborne polyurethane materials; Carry out construction technology research to reduce the impact of ambient temperature and humidity on the appearance of waterborne polyurethane film; Strengthen the research and development of special equipment for waterborne polyurethane.
Development history of automotive coatings
In the 64 year history of China's automobile industry, China's automobile coatings have been updated four times.
The current fourth generation automotive coatings are represented by the 4th and 5th generation cathodic electrophoretic coatings, high-quality acrylic resin coatings with acid rain resistance and scratch resistance, acrylic polyurethane coatings, metal and natural colors of the top coat, and coatings suitable for the three-layer coating system of cars. In recent years, with the introduction of car products and car body coating line, the world-famous automobile coating company has set up factories in China to meet the international car coating standards. Based on the different countries where car products are introduced, this generation of automotive coatings can be divided into Japanese system and European and American system.
Since the 1990s, European and American automobile factories have adopted environment-friendly automobile coatings to replace the traditional organic solvent automobile coatings in order to meet the environmental protection standards. By 2001, the proportion of cars with water-based intermediate coat and base color paint in the total output was 7% and 43% in North America respectively; Europe 32.5% and 36%. Among them, Germany has basically achieved hydration, with medium coating accounting for 80% and base color paint accounting for 93%. In Asia, only 1.5% of cars use waterborne primer.
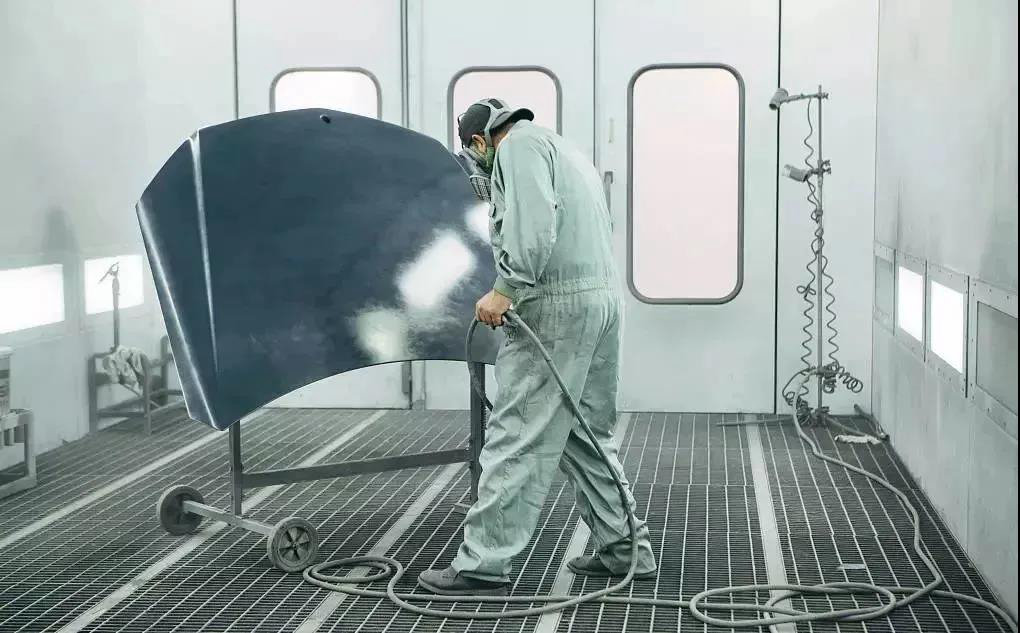
With the continuous development of the automobile market in the 21st century, consumers' demand for automobile consumption is becoming more and more mature. Personalization and diversification will become a new growth point. Under the highly competitive environment, automobile dealers must develop more automobile service projects and deeply tap the connotation of automobile culture to meet the needs of consumers and form individual competitive advantages. The comprehensive automobile trade service park, through the effective integration of resources and the introduction of new planning concepts and powerful service functions, realizes the diversification of automobile sales market, so it has strong vitality.
Although China's automobile industry is developing and growing, there is still a large gap in automobile coating and coating technology compared with industrial developed countries. In recent years, China's automobile manufacturing industry has built nearly 20 water-based coating lines, and many water-based coating lines will be put into construction one after another. The automobile industry takes the lead in creating the hydration of coatings, which can play a demonstration effect for the promotion and application of other industries. The development of waterborne coatings is beneficial to saving resources, improving environmental pollution, implementing cleaner production and achieving effective social and economic benefits. It can be predicted that with the continuous progress and innovation of coating and coating technology, there will be new breakthroughs in the price, performance, construction technology and reducing equipment investment of water-based coatings, and there will be greater development space in promoting and expanding the application field of water-based coatings.
Application of polyurethane coating in automobile industry
Polyurethane coating for auto parts and interior and exterior decoration
There are many kinds of automobile parts, interior and exterior trim parts, and the performance requirements of coatings are also different. If the bumper is coated with acrylic polyurethane (PU); Polyurethane (PU) primer for fender, side guard and bumper lower guard; Polyurethane (PU) coating for wheelhouse, spoiler and door handle; Two component polyurethane (PU) coatings used for automobile interior decoration by Austrian vianova resins company, etc.
Most of the car body parts and interior and exterior trim parts are all kinds of plastics, with a wide variety and growing trend. Due to different varieties of plastics, the adaptability requirements of substrate and coating are also different, so it is necessary to select appropriate coating for plastic parts coating. Polyurethane coating has a good material adaptability. With the renewal of vehicle plastics, polyurethane can adapt in most cases and has a broad application prospect.
Polyurethane coating for vehicle body
Primer
Cathodic electrophoretic paint is widely used in automotive primers all over the world. Cathodic electrophoretic polyurethane (PU) coatings can be prepared by using closed polyurethane (PU), polyester resin and epoxy resin. Now, in the process of hydration, first of all, the base color paint is hydrated, which can greatly reduce VOC emission. Nissan first started to use the 3C1B process of water-based primer in 2010, and used two-component polyurethane as varnish to meet the appearance requirements. In the 3C1B process of waterborne primer, Honda uses solvent-based two-component polyurethane to apply primer to improve the stone impact resistance of the system. It is reported that the intermediate primer has also begun to be hydrated, and Toyota and GM have begun to use the waterborne 3C1B process. In GM's future global process planning, the aqueous 3C1B process using two-component polyurethane varnish has become the standard.
Polyurethane (PU) electrophoretic coatings mainly include the following three categories: waterborne polyurethane (PU) resin electrophoretic paint, polyurethane (PU) modified waterborne resin electrophoretic paint and waterborne blocked polyisocyanate. Among them, water-based blocked polyisocyanates are most commonly used as crosslinking agents for various electrophoretic paints.
Cathodic electrophoretic polyurethane (PU) coating has excellent protection performance. According to the report, it still has good smoke resistance without anti-corrosion pigment, can meet the protection requirements of automobile body without perforation corrosion for 10 years, and the film is flat and plump. In addition, there is sometimes a stone impact resistant coating between the electrophoretic coating and the intermediate coating, which also belongs to the primer system. It is mainly to protect the parts vulnerable to the impact of gravel when the car is driving. Polyurethane (PU) coating has the best stone impact resistance, but the price is slightly more expensive.
Intermediate painting
Polyurethane (PU) intermediate paint (including various modified polyurethane intermediate paint) has many varieties and is widely used. Waterborne polyurethane (PU) intermediate paint, which meets the requirements of environmental protection, also has good performance, especially its flexibility and impact resistance are better than solvent based coatings. Polyurethane (PU) intermediate paint with excellent stone impact resistance and cold resistance is one of the development directions of automotive intermediate paint. Even if a small amount of polyurethane (PU) is used in the coating, its stone impact resistance is greatly improved. It has been found that adding a certain amount of polyurethane to the polyester amino resin system can significantly improve the elasticity, adhesion and stone impact resistance of the paint film.
Topcoat
The weather resistance of polyurethane topcoat is better than that of acrylic enamel, another widely used topcoat. The UV resistance and water permeability of polyurethane finish are stronger than acrylic enamel, and its comprehensive performance is also stronger than acrylic enamel. In addition, in previous years, a two-component waterborne polyurethane was developed, which can be directly attached to the metal without primer. It can be used on indoor and outdoor vehicles, and the anti-corrosion performance has been greatly improved. In 2008, when Bayer's innovative polyurethane coating technology was applied to modern concept cars, Hyundai launched a sporty "I-mode" car. Once the new car came out, it attracted the attention of consumers. What is most appreciated is that the innovative polyurethane coating has the ability of self-healing, can self repair automobile scratches, and has strong wear resistance. The plastic surface is protected by polyurethane coating, which gives the material surface luxurious appearance and delicate hand feel.
Polyurethane touch up paint
The profit of touch up paint is the highest compared with other vehicle coatings. Most of the repair paint is sold in 4S stores. The prices of primary sales and secondary sales are different. The average one-time sales price of foreign brand repair paint is about 70-85 yuan / kg. The difference in color will lead to the difference in price.
Black, white → red, yellow → pearlescent powder
Domestic repair paint has certain advantages in price. The quality is close to that of imported products, and the price is only 1 / 2-2 / 3 of that of imported products. Similarly, the competition is very fierce.
At first, natural resin paint was used for automobile repair paint, and then nitro paint and alkyd resin paint were gradually developed. In the 1970s, solvent based two-component polyurethane coatings entered the automotive touch up paint market and gradually became the leading product in the automotive touch up paint market. In the 1990s, a two-component polyurethane repair paint with high solid content was developed. It is reported that 138000 tons of polyurethane automotive touch up paint were sold in Western Europe alone in 1994. Around 2006, solvent based two-component polyurethane coatings accounted for about 86% of the market share in Western Europe. The waterborne two-component polyurethane coating for automobile repair has been commercialized, and its VOC is very low, which can meet the requirements of any strict solvent emission regulations.
The original automobile paint requires the film to have good gloss, fast drying, good water resistance, solvent resistance and aging resistance. In addition to these properties, the automotive repair paint must also be able to cure at low temperature, and the two-component polyurethane coating can meet these requirements. The two-component polyurethane coating composed of acrylate polyols and polyisocyanates can be cured at room temperature or low temperature, and can be used on automotive metals, plastics, wood and other substrates, This kind of coatings cause serious harm to the environment because of the use of more volatile organic compounds as solvents.
With the introduction of national standards for limiting volatile organic compounds, it poses a challenge to the traditional solvent based polyurethane coatings. In recent years, waterborne two-component polyurethane coatings were developed and achieved success. Additives such as leveling agent, defoamer, catalyst, light stabilizer, thickener and organic cosolvent are usually added to the hydroxyl containing components of waterborne two-component polyurethane coating for automobile repair paint, and then mixed with polyisocyanate components, water is added to adjust the viscosity, and spraying method is used for construction. The waterborne two-component polyurethane coating for automobile repair has long been commercialized. Its VOC is much lower than that of solvent polyurethane coating, which can meet any strict solvent emission regulations. Waterborne two-component polyurethane coatings are gradually replacing the traditional solvent based coatings. With the increasingly strict environmental protection regulations, it will occupy a larger market share.
Policy: the development of waterborne coatings is an inevitable trend
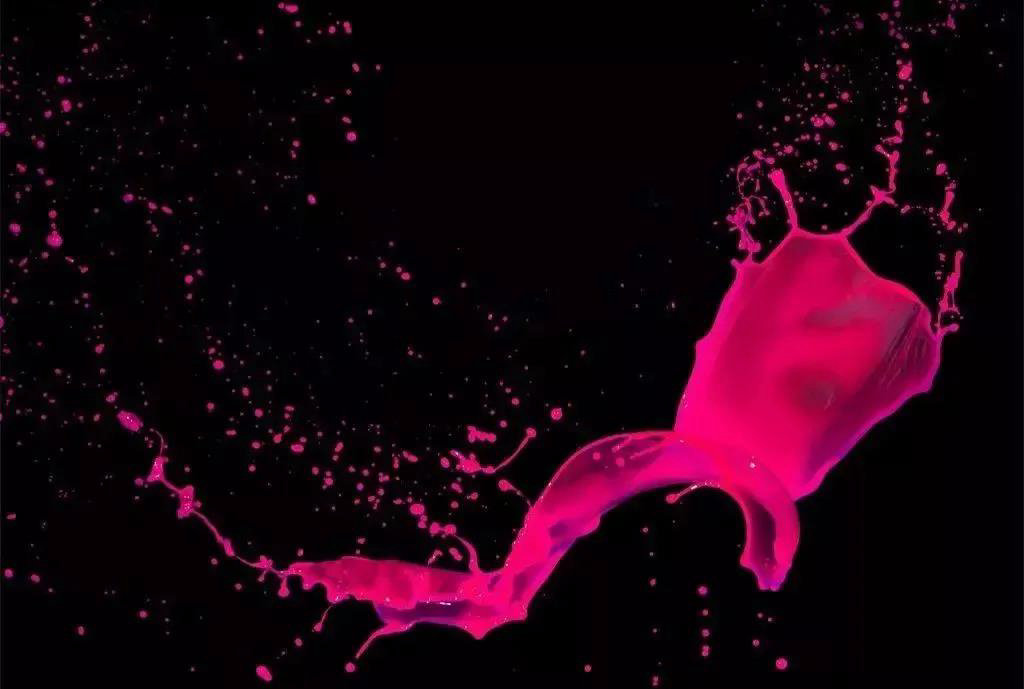
In July 2016, the Ministry of industry and information technology and the Ministry of Finance issued the action plan for VOC reduction in key industries, encouraging relevant industry associations, scientific research institutes and consulting institutions to study and formulate the VOCs reduction roadmap of the industry and promote the VOC reduction in key industries. China Automotive Technology Research Center has formulated the road map for VOC reduction in the automotive industry, and put forward the objectives, technical routes and demonstration cases of VOCs reduction in the automotive industry.
It is reported that the high concentration, high intensity and long duration of VOCs emission in the production of automobiles and their parts are one of the important factors causing atmospheric VOCs Pollution. Since the 12th Five Year Plan, the proportion of environmental protection coatings used in China's automobile industry has been increasing, and the VOCs emission indicators of some new coating production lines have reached the world-class level. However, more than 10 million automotive products are still produced by traditional solvent based coating process every year, and a large amount of VOCs is emitted in the manufacturing process. At the same time, VOCs released from car interior will also have a certain impact on the health of drivers and passengers.
According to the action plan, in order to guide the technological progress of the industry, formulate VOCs emission targets for the automotive industry. From December 31, 2018, VOCs emission per unit coating area will be 35g / ㎡ for passenger cars, 75g / ㎡ for truck cockpit, 90g / ㎡ for truck carriage and 180g / ㎡ for passenger cars. From December 31, 2020, VOCs emission per unit coating area is 30g / m2 for passenger cars, 65g / m2 for truck cockpit, 70g / m2 for truck carriage and 150g / m2 for passenger cars.
It is reported that the automobile coating process system supporting various coatings can make the emission of organic solvent (VOC) meet the environmental protection requirements (below 35 g / ㎡) only by adopting the system of water-based intermediate coating and water-based primer and two-component high solid partial gloss varnish, water-based gloss varnish or powder gloss varnish.
Conclusion:
The characteristics of China's automotive coating industry are: high regional concentration and large gap; Backward technology and low profit; The support of the government and industry associations will not be reduced. The distribution areas of China's coating industry are still the Yangtze River Delta, the Pearl River Delta and the Bohai rim, which account for 80% of the national coating industry. However, the quality and variety of automotive coatings in China are still lagging behind. The real domestic famous brands are few and control the market share is very small.
Polyurethane coatings are more and more widely used in automobile industry, especially waterborne, high solid and powdered polyurethane coatings are the future development direction. Among them, waterborne two-component polyurethane coatings have been commercialized, but the price is still relatively high. With the national tightening of VOCs emission per unit coating area of automobile, it will drive the rapid development of waterborne coatings. The disadvantage of domestic brands is that their profits are often less than 15%, which is even more difficult when the price of raw materials rises. How to grasp the color trend and obtain a certain market in the high profit field of touch up paint is what we need to think about. At the same time, with the transformation of technology and the development of hydration, the automotive coating industry will usher in a fierce reshuffle.
Source: water paint assistant